1- Purpose
The purpose of this work is to investigate the effects of activating fluxes and welding parameter to the penetration and depth-to-width ratio (DWR) of weld bead of Inconel 718 alloy welds in the tungsten inert gas (TIG) weldingprocess. In the activating flux with TIG (A-TIG) welding process, the single-component fluxes used in the initial experiment were SiO2, NiO, MoO3, Cr2O3, TiO2, MnO2, ZnO, and MoS2. Based on the higher DWR of weld bead, four fluxes were selected to create six new mixtures using 50% of each original flux. The A-TIG weldment coated 50% SiO2 + 50% MoO3 flux and 75° of electrode tip angle were provided with better welding performance. In addition, the experimental procedure of flux-bounded TIG (FB-TIG) welding with the same welding conditions and flux produced full penetration of weld bead on a 6.35 mm thickness of Inconel 718 alloy plate with single pass weld.
2- Method
The purpose of this work is to investigate the effects of activating fluxes and welding parameter to the penetration and depth-to-width ratio (DWR) of weld bead of Inconel 718 alloy welds in the tungsten inert gas (TIG) weldingprocess. In the activating flux with TIG (A-TIG) welding process, the single-component fluxes used in the initial experiment were SiO2, NiO, MoO3, Cr2O3, TiO2, MnO2, ZnO, and MoS2. Based on the higher DWR of weld bead, four fluxes were selected to create six new mixtures using 50% of each original flux. The A-TIG weldment coated 50% SiO2 + 50% MoO3 flux and 75° of electrode tip angle were provided with better welding performance. In addition, the experimental procedure of flux-bounded TIG (FB-TIG) welding with the same welding conditions and flux produced full penetration of weld bead on a 6.35 mm thickness of Inconel 718 alloy plate with single pass weld.
3- Results
The purpose of this work is to investigate the effects of activating fluxes and welding parameter to the penetration and depth-to-width ratio (DWR) of weld bead of Inconel 718 alloy welds in the tungsten inert gas (TIG) weldingprocess. In the activating flux with TIG (A-TIG) welding process, the single-component fluxes used in the initial experiment were SiO2, NiO, MoO3, Cr2O3, TiO2, MnO2, ZnO, and MoS2. Based on the higher DWR of weld bead, four fluxes were selected to create six new mixtures using 50% of each original flux. The A-TIG weldment coated 50% SiO2 + 50% MoO3 flux and 75° of electrode tip angle were provided with better welding performance. In addition, the experimental procedure of flux-bounded TIG (FB-TIG) welding with the same welding conditions and flux produced full penetration of weld bead on a 6.35 mm thickness of Inconel 718 alloy plate with single pass weld.
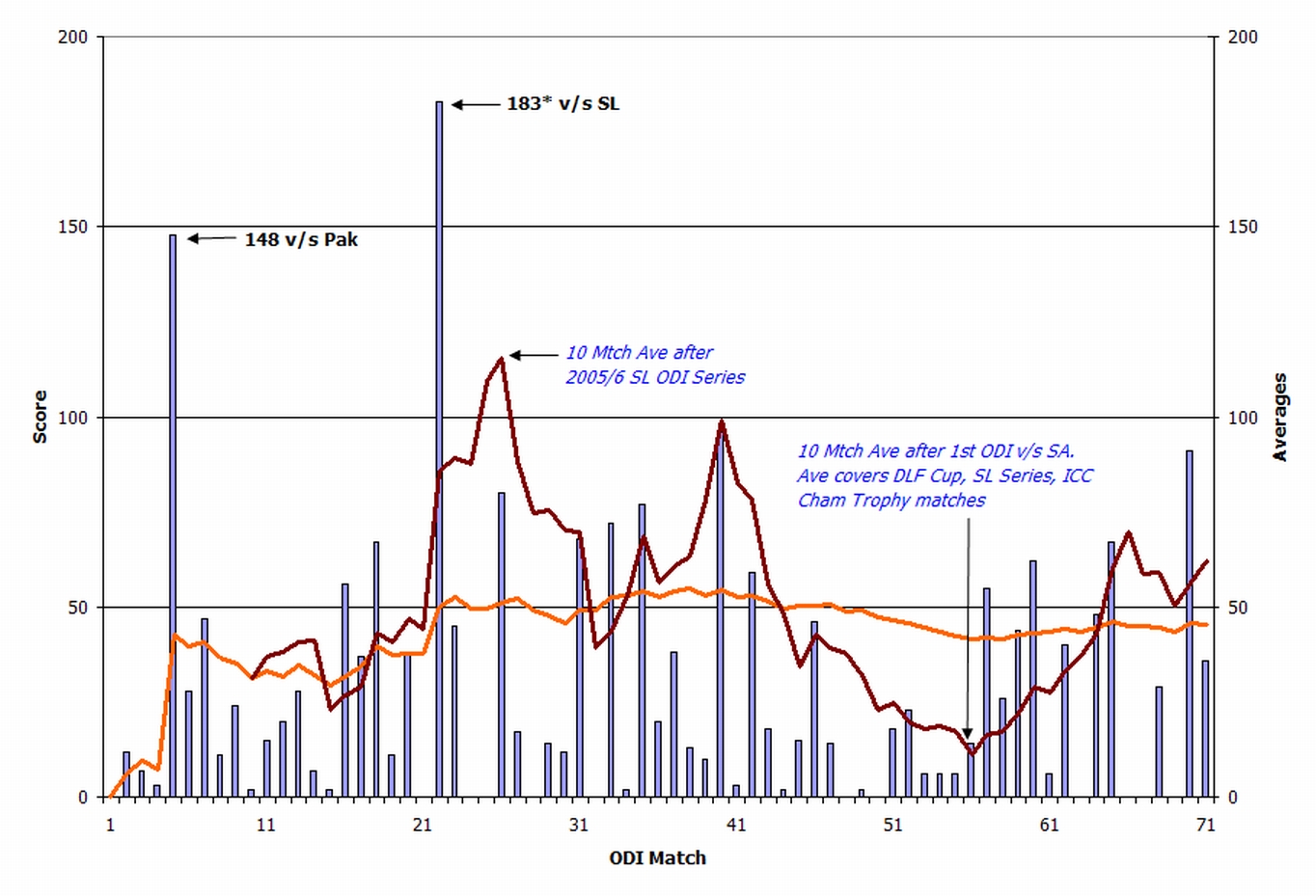
Flux produced full penetration of weld bead on a 6.35 mm thickness of Inconel 718 alloy plate with single pass weld.